Gift boxes are high-end printed products. The production and processing of finished products requires a lot of effort from the beginning of the design concept. Designers must constantly think deeply about how to bring the gift box design to a higher level from the aspects of material, shape, craftsmanship, function, etc., so as to have more online sales and temptation. In this article, we are explore the world of different special finishes and help you select the best special finish on your gift box printing.
The Benefits of Apply Special Finishes on Gift Box
1. Increase the product value. Because beautiful gift box will give many people such of feel that its collect value is very high. So it is a means of increasing the value of goods. More and more businesses will use high quality gift box to attract more customers and make them choose their products the first time.
2. Improve printing quality. The combination of multiple processes are combine the advantages of various printing processes. Therefore, this combined printing method can ensure the printing effect of printed gift box to the greatest extent. Then meeting people’s growing sensory requirements. Meanwhile, improving the printing quality of the printing factory, to achieve improve production efficiency and reduce costs. The combination of multiple processes also includes printing and post-press processes. During gift box production, printing and post-press are completed at one time, and the finished product is produced directly, which can greatly reduce costs.
3. Achieve various design effect. Using special finishes on the gift box, designers and businesses can bold use of various unique effects expand visual design ideas. Then find the balance between vision and touch, to select the suitable special finish apply on the gift box, and making their gift box standout from the competitors.
6 Common Special Finishes in Customized Gift Box Packaging
1. Lamination
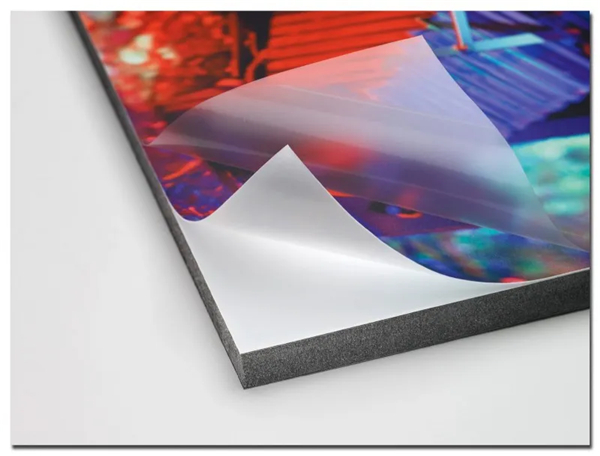
Lamination is the most basic post-press. It refers to the transparent plastic film being pasted onto the surface of the gift box through hot pressing, making the gift box look extremely shiny and improving the product texture and packaging effect. At the same time, after laminating, the pressure resistance and wear resistance of the surface will be improved. It can increase the quality of the gift box and better protect the goods.
Lamination include: glossy lamination and matte lamination. Glossy lamination can make the surface of the product brighter and enhance the expressiveness of the product. The surface of the product covered with matte lamination will not reflect light, make it looks elegant and enhances the image of the packaging product. We usually recommend the paper over 200gsm for laminating.
2. Foil stamping
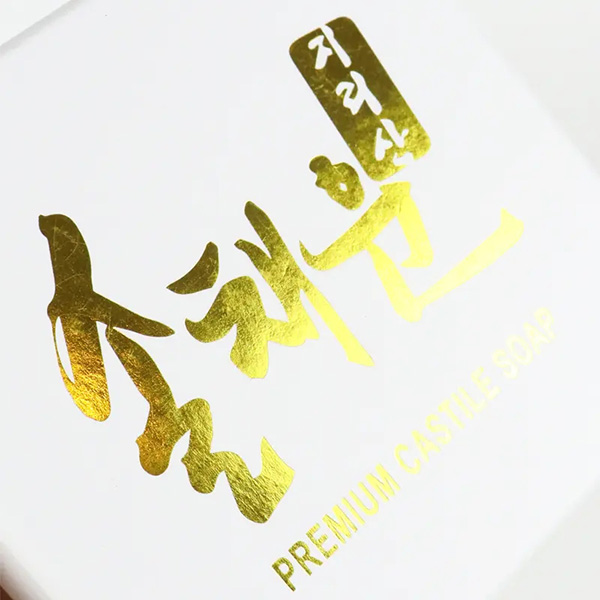
The hot stamping, also known as foil stamping, is the process of using a certain amount of pressure and temperature to press the printed matter and hot stamping plate on the template. Through heating and foiling, gift box surface will be printed with golden patterns and text.
In the packaging design of gift boxes, designers often use the hot stamping process for the brand logo and important information. For example, when custom jewelry gift box, with foil stamping to highlight the logo, allowing consumers to see the product information at a glance and deepen their impression.
The overall look of the gift box after hot stamping, make it looks very high-end and elegant. Even if the gift box does not use complicated colors and elements, a simple hot stamping process can instantly improve the overall level. It is a very quick way to improve the packaging effect of the customized gift box.
In addition, aluminum foil has excellent physical and chemical properties and can protect printed matter. Thus, the hot stamping process is widely used in modern customized packaging box printing, and many materials can be hot stamped. Especially for high-end papers, such as Kraft paper and black cardboard that are not suitable for printing, the hot stamping process is very suitable. Generally, we use hot stamping and silver hot stamping processes. But we can also provide other colors, like red foil stamping, laser gold, based on customer needs.
3. Emboss and deboss
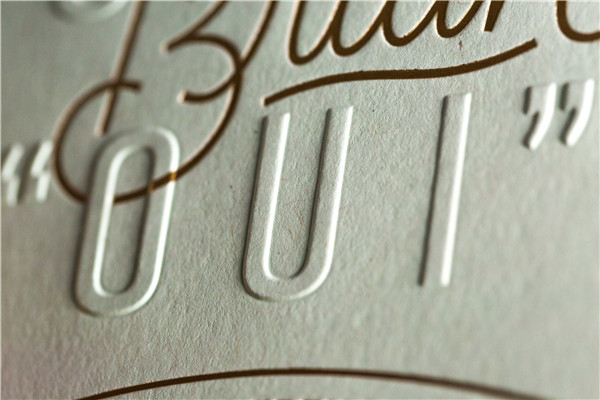
Emboss and deboss processing is a special method for processing product packaging boxes. Generally speaking, emboss or deboss uses a mold to deform the printed matter under a certain amount of pressure. So that the entire product surface presents a relief-like emboss and deboss feeling, which enhances the difference of the product. The emboss and deboss patterns can be made into various shades of patterns according to the needs of customers. They just like the reliefs in sculptures, which increase the overall three-dimensional sense and visual impact of the product packaging box.
Different textures can bring different decorative art effects to the surface of the gift box. For example, the surface of a tea gift box can be embossed with fresh water patterns. The tea give people the feeling of fresh and elegant fragrance. The combination of fresh water lines and appropriate colors looks very good. The elegance and simplicity can highlight the temperament of tea products. Increasing the beauty and added value of the product and making the gift box more attractive and beautiful.
4. UV coating
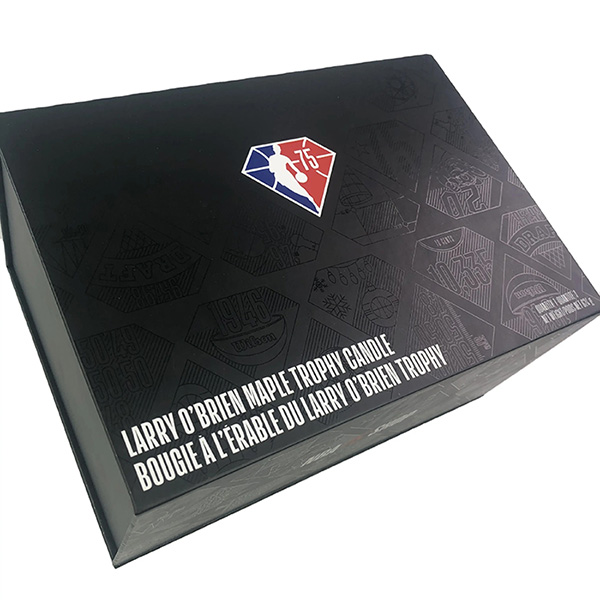
UV coating. UV coating is a process that relies on ultraviolet irradiation to dry and solidify ink. It is now the most commonly used printing process. Use it to custom gift box packaging, the gift box surface will have a bright layer of uv ink, which looks very smooth and textured. UV coating adds a three-dimensional and high-end feel to the surface, as well as increase the product value. Moreover, UV printing has the characteristics of short production cycle, clear printing dots, and strong corrosion resistance. It is very conducive to the rapid circulation of gift boxes after production and enhancing the quality of gift boxes.
5. Varnish
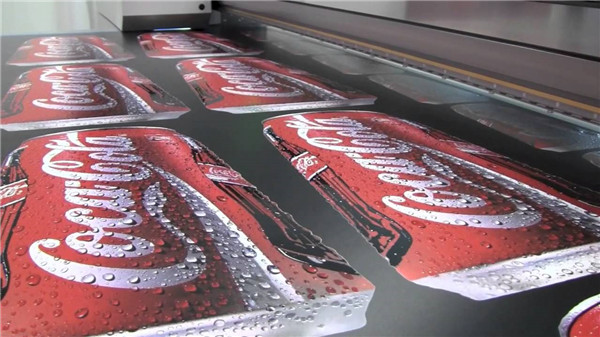
Varnish can effectively protect the surface of packaging gift boxes. As the name suggests, “varnish” is to spray a layer of colorless transparent paint on the surface of printed matter. Then to form a certain gloss on the surface of printed airplane boxes and product gift boxes, and to play a role in waterproofing and oil-proofing on packaging surface. At the same time, because the printing is isolated from the air, it has a good blocking effect and can keep the color of the printed surface bright. Making the color of the product packaging box can be maintained for a long time.
6. Die cutting
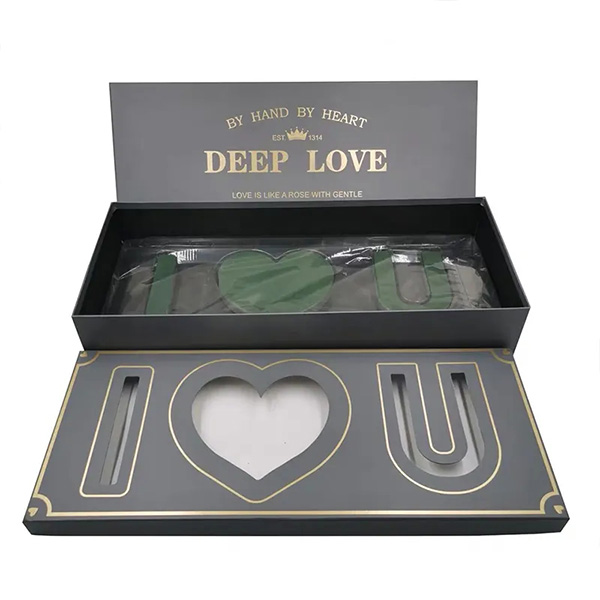
The die-cut process is also known as die-cutting, buckling, etc. When the gift box needs to be cut into a certain shape, we can do it through the die-cutting process. Die-cutting is a method in which steel blades are arranged into molds (or steel plates are carved into molds), frames, etc., the paper is cut into a certain shape on the die-cutting machine, and then the waste is removed. This method can provide 3D effect and various personalized options for packaging.
The above 6 special finishes are widely used in custom gift box printing, which can make the gift box packaging look high-end and textured. The special finish enriches the texture of the gift box and increases the added value of the product. Consumers will have a good impression on the product itself due to the exquisite packaging. Thereby achieving the expected goal of using printing technology, capturing the hearts and pockets of consumers with beautiful and exquisite packaging, and closing transactions.
If you are ready to custom print your own gift box to improve your brand value and leave depth impress on your target audience, contact us today. Our pursuit of details and rich experience of custom packaging, that will make sure to help you bring your dream to life.